Effective volume manufacturing capabilities determine a company’s resilience and competitive edge in today’s volatile global marketplace. With ongoing supply chain disruptions, labor shortages, and inflationary pressures affecting manufacturers worldwide, mastering volume manufacturing strategies has never been more crucial. To thrive in this environment, companies must adopt a holistic approach that integrates advanced technologies, agile methodologies, and cross-functional collaboration. Volume manufacturing refers to producing goods in substantial quantities, requiring specialized approaches to optimize throughput, quality, and cost-effectiveness while navigating international logistics challenges. Understanding these core principles helps businesses implement systems that scale effectively across global operations.
Foundational Elements of Effective Volume Manufacturing Systems
Successful volume manufacturing begins with thoughtful planning and infrastructure development that accounts for today’s multi-regional sourcing reality. Production facilities explicitly designed for volume manufacturing feature optimized layouts that minimize material handling and maximize worker efficiency—increasingly crucial as labor costs rise globally. The physical arrangement of equipment in volume manufacturing environments follows logical process flows, reducing transit times and work-in-progress inventory while enabling greater flexibility.
Equipment selection represents another critical aspect of volume manufacturing planning in 2025’s manufacturing landscape. Machinery for volume manufacturing must demonstrate reliability, consistency, and serviceability to support continuous operations, especially when technical support may be limited in certain regions. Unlike prototype or low-volume equipment, volume manufacturing systems often incorporate redundant capabilities to prevent production bottlenecks and maintain consistent output even during maintenance activities—a crucial consideration for facilities in developing markets.
Process Optimization and Continuous Improvement Methodologies
Volume manufacturing excellence requires rigorous process optimization to eliminate waste and variation, which becomes significant as material costs fluctuate and availability becomes less predictable. Techniques like Six Sigma and lean manufacturing provide structured approaches to enhancing volume manufacturing operations across diverse cultural contexts. These methodologies help identify opportunities for cycle time reduction, quality improvement, and cost savings throughout the volume manufacturing process, regardless of facility location.
Data collection and analysis play increasingly essential roles in modern volume manufacturing environments, enabling real-time oversight of global operations. Advanced volume manufacturing facilities implement comprehensive monitoring systems that capture real-time production metrics across multiple locations. These systems allow predictive maintenance scheduling, process drift detection, and continuous optimization of volume manufacturing parameters based on statistical analysis rather than subjective evaluation—providing consistency across international manufacturing footprints.
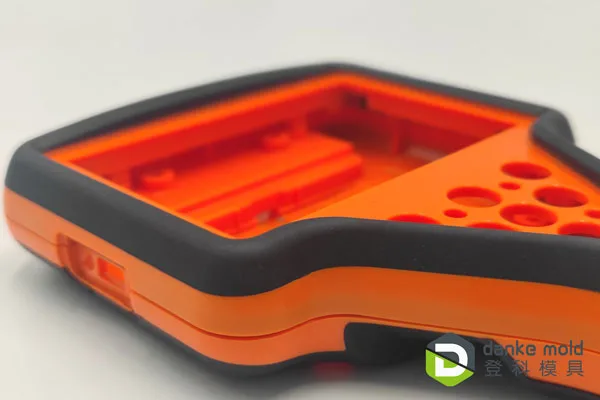
Over molding parts
Supply Chain Integration and Material Management
The success of any volume manufacturing operation depends heavily on robust supply chain management—a challenge intensified by recent global disruptions. Procurement strategies for volume manufacturing now emphasize geographical diversification, supplier partnerships, quality agreements, and reliable delivery scheduling. Creating redundancy in critical material sourcing protects volume manufacturing operations from unexpected disruptions that have become increasingly common since 2020.
Inventory management presents unique challenges in volume manufacturing contexts, especially when balancing just-in-time principles with the reality of extended international shipping timelines. Just-in-time and lean principles help minimize carrying costs while ensuring material availability for uninterrupted production. Sophisticated volume manufacturing operations employ automated inventory systems that maintain optimal stock levels based on production forecasts, lead times, and historical consumption patterns while accounting for longer transit times in global logistics networks.
Quality Assurance Strategies at Scale
Maintaining consistent quality while operating at high volumes requires systematized approaches to quality control that function effectively across diverse manufacturing environments. Volume manufacturing quality systems typically incorporate a combination of in-process monitoring, statistical sampling, and automated inspection technologies. This multi-layered approach ensures that volume manufacturing outputs meet all specifications without requiring 100% manual inspection, which would create bottlenecks in high-throughput environments.
Traceability represents another critical aspect of quality management in volume manufacturing, particularly for products crossing international borders. Modern volume manufacturing operations implement comprehensive tracking systems that maintain associations between specific products, their component materials, process parameters, and quality data. This capability proves essential when addressing potential quality issues in volume manufacturing, allowing for targeted containment actions rather than broad recalls—critical for minimizing financial impact in global distribution networks.
Danke Mold: Your Global Volume Manufacturing Partner
With our extensive engineering knowledge and strategic locations, Danke Mold provides volume manufacturing solutions that balance quality, cost, and speed for companies worldwide. Our Design For Manufacture (DFM) assessments ensure every project maximizes efficiency—we don’t just follow CAD files, we optimize every aspect of your design for volume manufacturing success in today’s challenging global environment.
As overseas outsourcing continues to evolve in response to changing economic conditions, trade policies, and logistics challenges, our volume manufacturing expertise offers stability and predictability. Our facilities feature the latest technology and highly skilled staff capable of managing complex projects, while our communication systems ensure seamless collaboration across time zones.
Whether navigating supply chain constraints, seeking cost advantages, or needing to scale production rapidly, our volume manufacturing capabilities offer the flexibility and reliability your business demands. Contact Danke Mold today for a consultation and discover how our global volume manufacturing solutions can transform your production strategy!