Rapid Tooling & Prototyping Injection
Molding Service
-
Aggressive Turn-Around
-
As Fast As in 15 Days
-
Instant Email Response
Rapid Tooling and Prototype Injection Molding
Danke Mold provides prototyping plastic injection molding services in aggressive turn-around time. Our engineers, will generally consider the technical concerns, lead time, quality & quantity requirement, and cost to provide a most suitable prototyping injection molding option for you.
To our technical innovation customers, we take the speed as the most important value. Our instant response, deep insight at the technical concerns, mutual rapid tooling manufacturing process, & professional project management will truly benefit our customers.
What will be our prototyping injection molding services used for?
- Low-volume production
- Engineering verification
- Tooling structure verification
- Materials trial & testing
- Bridge tooling
Prototyping Injection Molding & rapid tooling service is widely used all over the world.
Our rapid Prototype Injection Molding Service is serving the technical innovation companies all over the world.
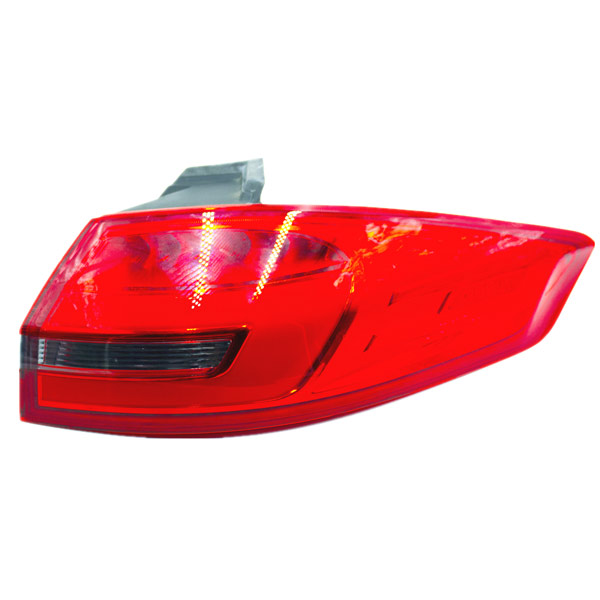
Automotive
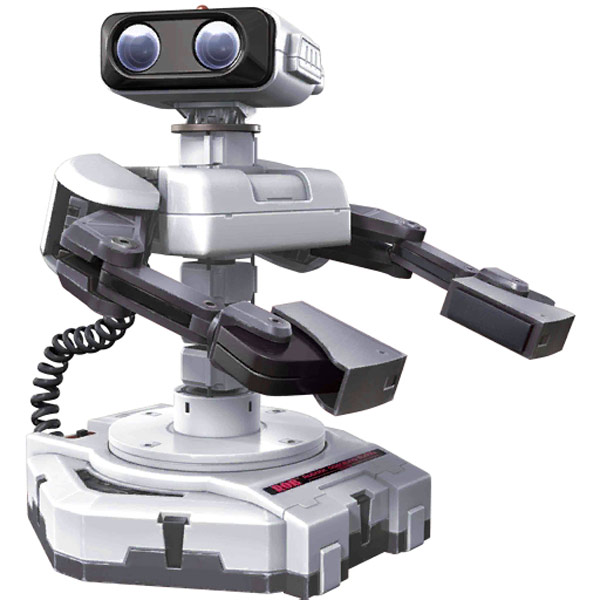
Robotics
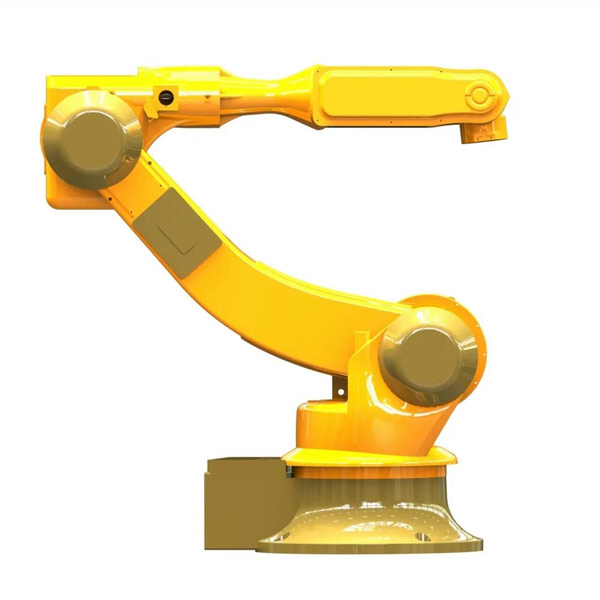
Industrial
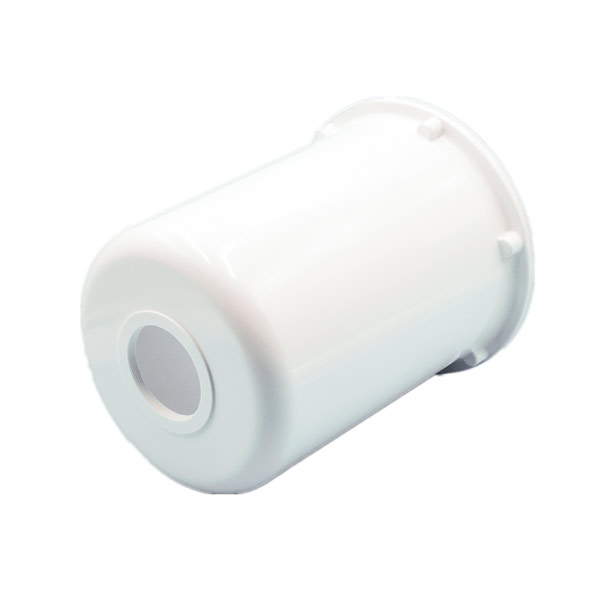
Communication
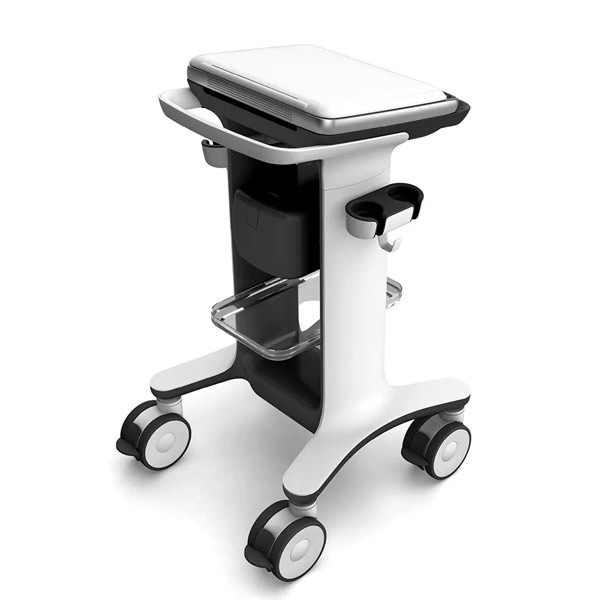
Medical
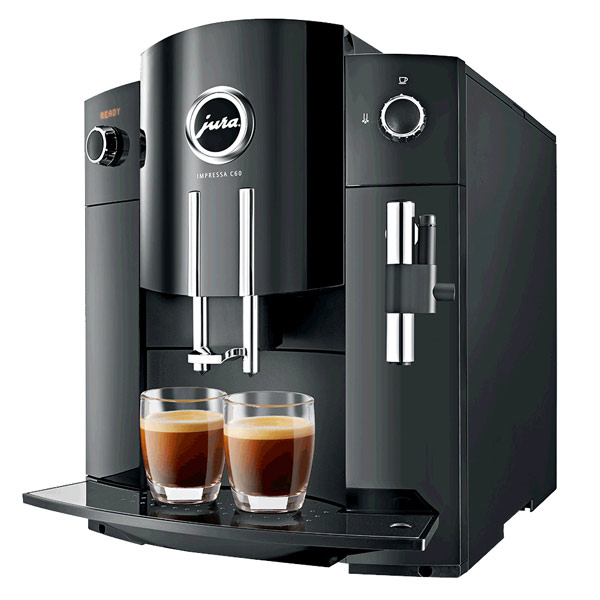
Consuming Electronics
Prototyping Plastic Injection Molding Capacity
At the prototyping stage of product development, we would have a lot of uncertainty for testing. Danke Mold is flexible to our customer’s request.
Plastic Injection Molding Material
- All material certified;
- Material supplied by customer available;
- Specific material sourced available from certified supplier;
- Muti-material trial available;
- Material suggestion available;
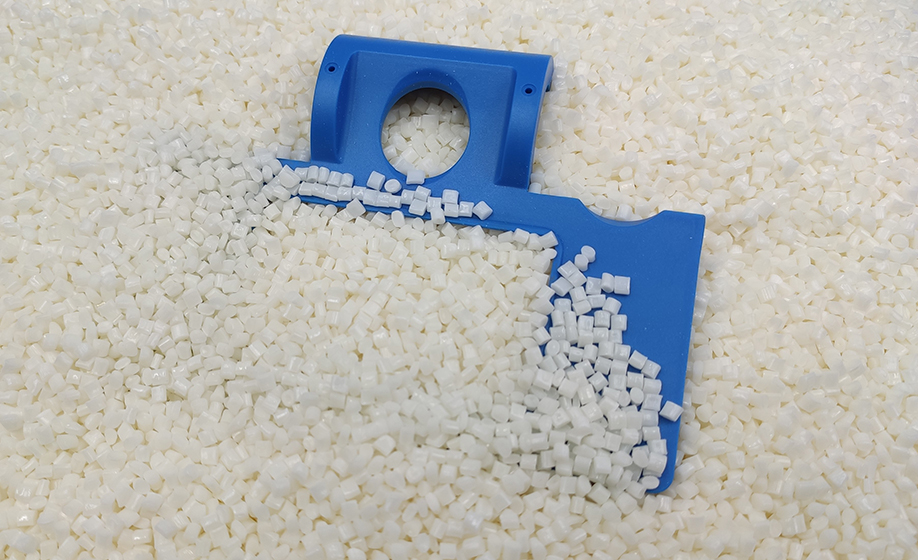
Injection Molding Tooling Surface Finish
- Polishing;
- High polish for glossy/high glossy;
- VDI sparking surface;
- MT texture equivalent;
- Mold-Tech texture
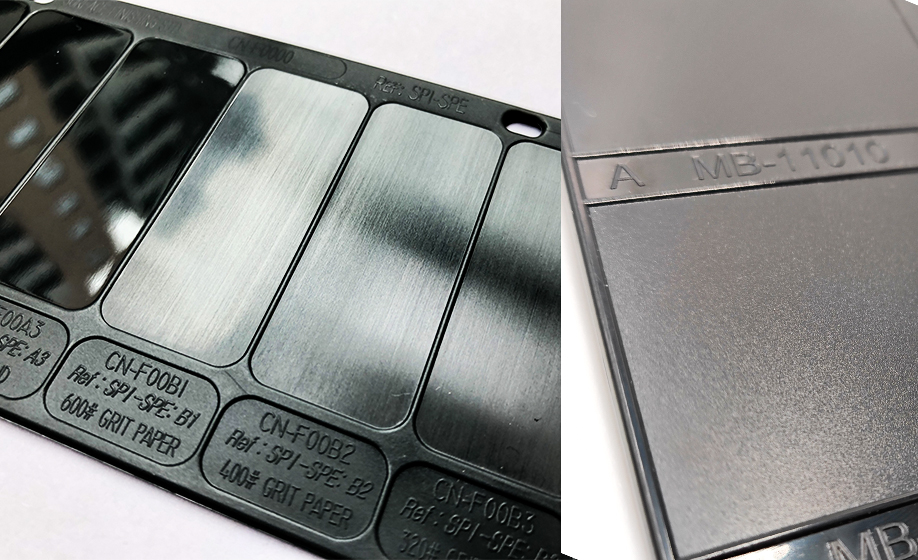
Plastic Injection Molding Color
- Pantone Color to follow;
- RAL Color to follow;
- Existing samples to follow;
- Samples with different colors available;
- Production with different color available;
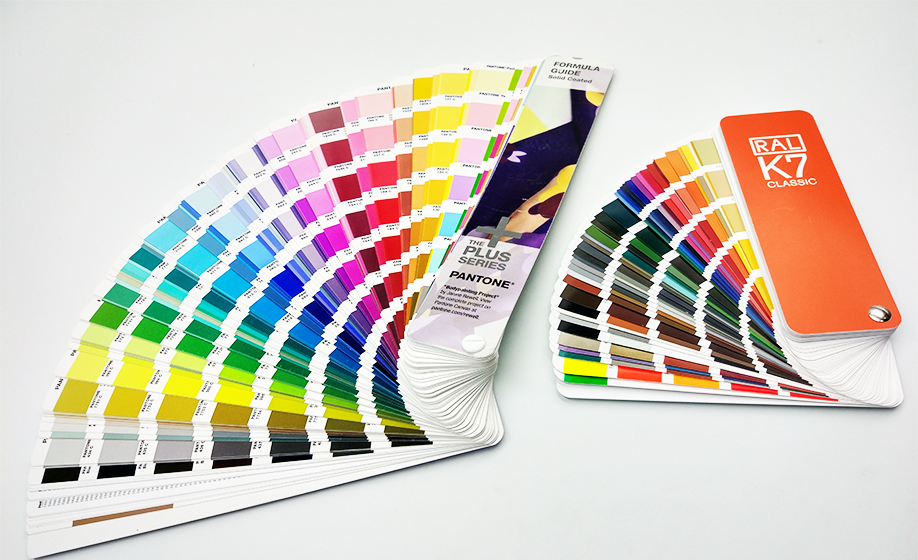
Injection Molding Part Size
- Length: 1100mm;
- Width: 550mm;
- Heigh: 300mm;
- Weight: 2.5kg;
- Quantity: NO MOQ
- Tolerance: +/- 0.02mm
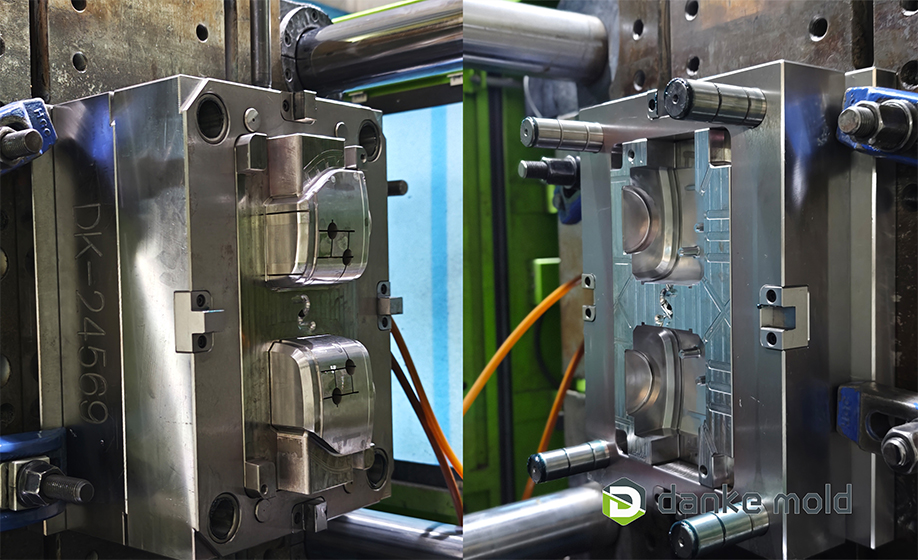
Injection Molding Tooling Steel
- Soft steel: P20, C50;
- Aluminum 7075 for simple parts;
- NAK 80 for high glossy parts;
- Harden steel available upon request;
- Heat treatment available;
- Tooling Surface Nicole Plating available;
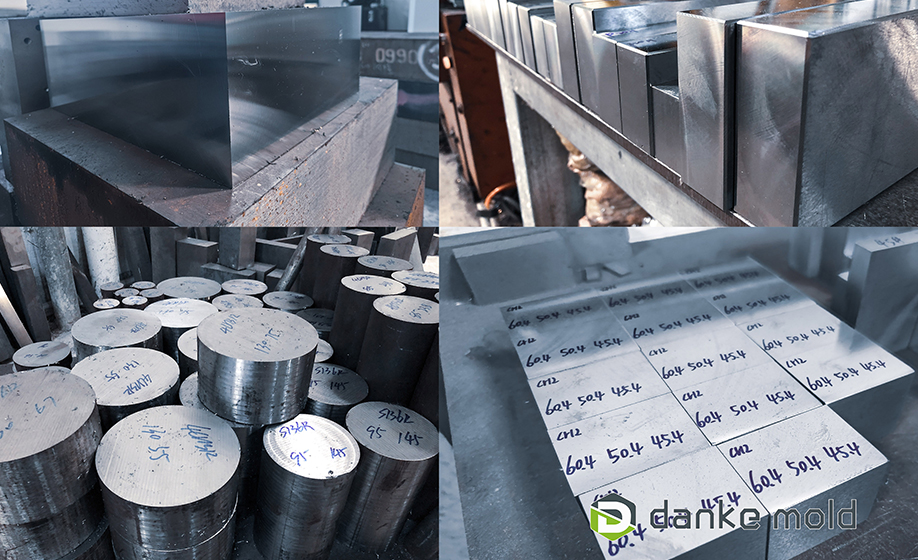
Prototyping Injection Molding Tooling Structure
- 2 Plates / 3 Plates cold runner injection mold;
- Reversal tooling structure available;
- Hot runner available for tooling structure verification;
- Hand-loaded inserts applied for undercuts;
- Over-molding & insert molding available;
- Hydraulic slider available for deep core;
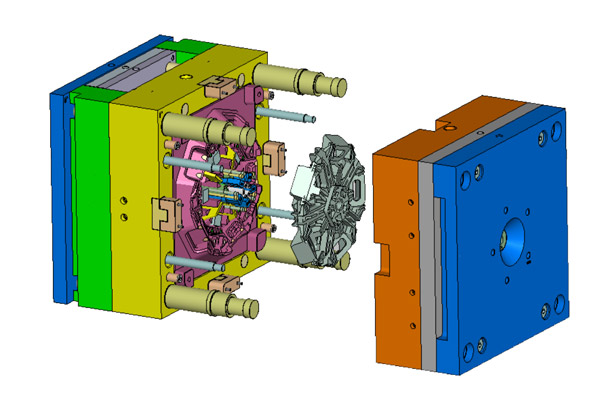
How Can We Faster at Our Prototyping Plastic Injection Molding Projects?
For most of the technical innovation projects, speed is one of the most important values.
Danke Mold provides rapid tooling & Prototyping Plastic Injection Molding services.
In order to being faster & more reliable, we’re keen on improving our project management, injection molding fabrication process, rapid tooling structure, and our communication.
Professional Project Management for Prototyping Injection Molding Project
- Thorough and insight DFM analysis;
- Potential Technical risk forecasted, so that make sufficient preparation & quick decision;
- Flow chart for injection tooling fabrication schedule control;
- All green line manufacturing process schedule;
- Rich experience tooling engineer daily on-site follow up;
- Swift engineering solutions with preparation;
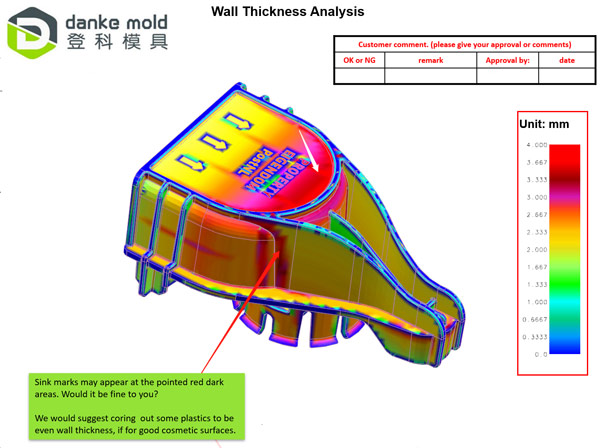
Rapid & In Parallel Plastic Injection Molding tooling Fabrication Process
- Tooling Insert steel upfront stock before machining start;
- Soft steel tooling inserts for easier CNC machining;
- For a big tooling core, split it into several cores, for in parallel machining;
- Carbon EDM sparking instead of Coper EDM sparking;
- Each tooling component is waiting no more than 6 hours between different process;
- At a same process, multi machines working in parallel for a same tooling;
- Deep hole drilling, wire cutting will be processing in parallel for different tooling components, different tools;
- CNC machining, EDM sparking will be processing in parallel for different tooling components, different tools;
- Surface Polishing, tooling assembly & mold trial will be process in parallel for different tooling components, different tools;
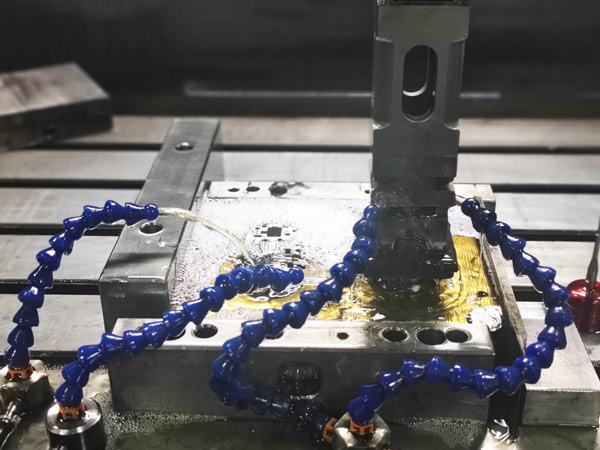
Simplified Injection Molding Tooling Structure
- Soft steel for tooling inserts;
- Or Aluminum 7075, if feasible;
- MUD mold base or common based used;
- Or integrated tooling inserts for the A/B Plates(without Mold Base);
- Hand loaded inserts for the undercuts if feasible;
- Sprue gate, fan gate, edge gate preferred for better material flow;
- Single Cavity mold or Family mold as many as possible;
- Straight cooling line, unless cosmetic or engineering concerns;
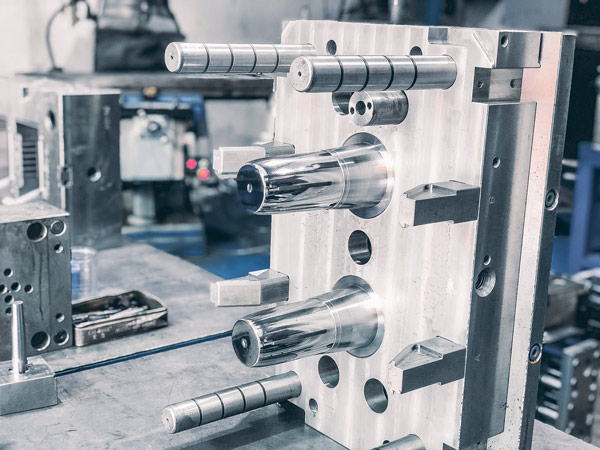
Instant & Professional Communication
- Quotation with DFM analysis;
- Instant email communication;
- Engineering negotiation response every day;
- Video meeting to simplify the communication;
- Upfront for days at project arrangement, so that no delay at processing;
- Upfront information at potential issue, so that our customers make earlier decision;
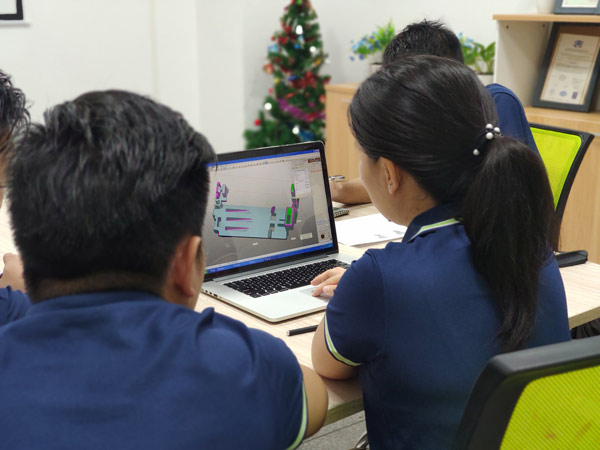
Some Prototyping Injection Molding Projects
We have worked hundreds of prototyping injection molding projects, with competitive prices and aggressive turn-around time.
Following would be the brief information of some projects:
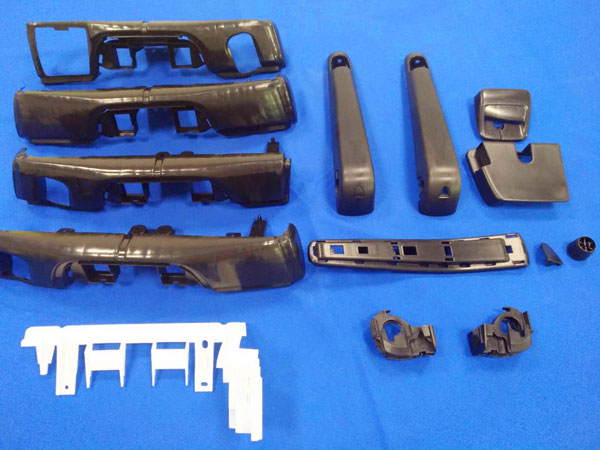
General Introduction:12 sets of prototype molds for 16 parts were finished within 1 month
Industry:Automotive
T1 Samples’ Lead Time:28days
General Tooling Price:USD 16,000
Maximum Part Size::170*99*40mm
Part Material:HDPE, POM, PA66+30%GF
Tooling Life Time:50,000 cycles
Tooling Material:P20/P20
Tooling Structure:Manual insert, sliders, cold runner
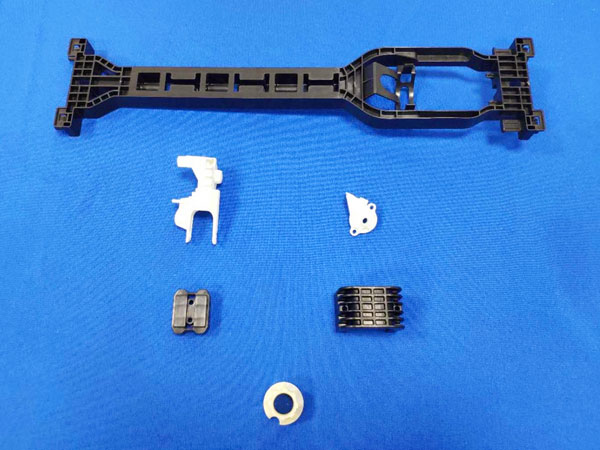
General Introduction:4 sets of prototype molds for 6 parts with lots of tolerances
Industry:Automotive
T1 Samples’ Lead Time:35days
General Tooling Price:USD 20,000
Maximum Part Size:420*100*50mm
Part Material:HDPE, POM, PA66+30%GF
Tooling Life Time:50,000 cycles
Tooling Material:P20/P20
Tooling Structure:Manual insert, sliders, cold runner
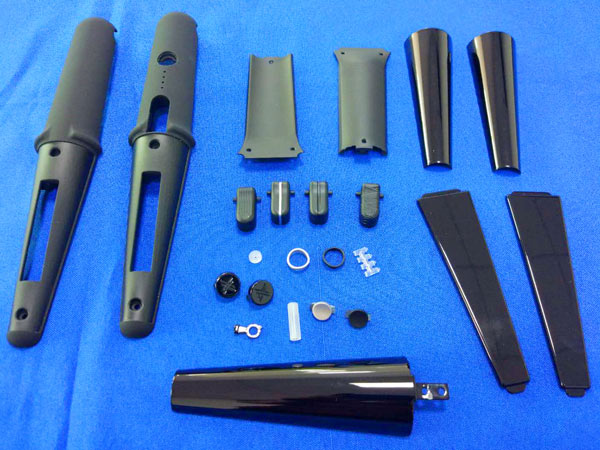
General Introduction:Hair style machine from prototype making to injection molding
Industry:Consuming Product
T1 Samples’ Lead Time:35days
General Tooling Price:USD 12,000
Maximum Part Size:250*40*25mm
Part Material:PET+30%GF
Tooling Life Time:50,000 cycles
Tooling Material:P20/P20
Tooling Structure:Manual insert, sliders, cold runner
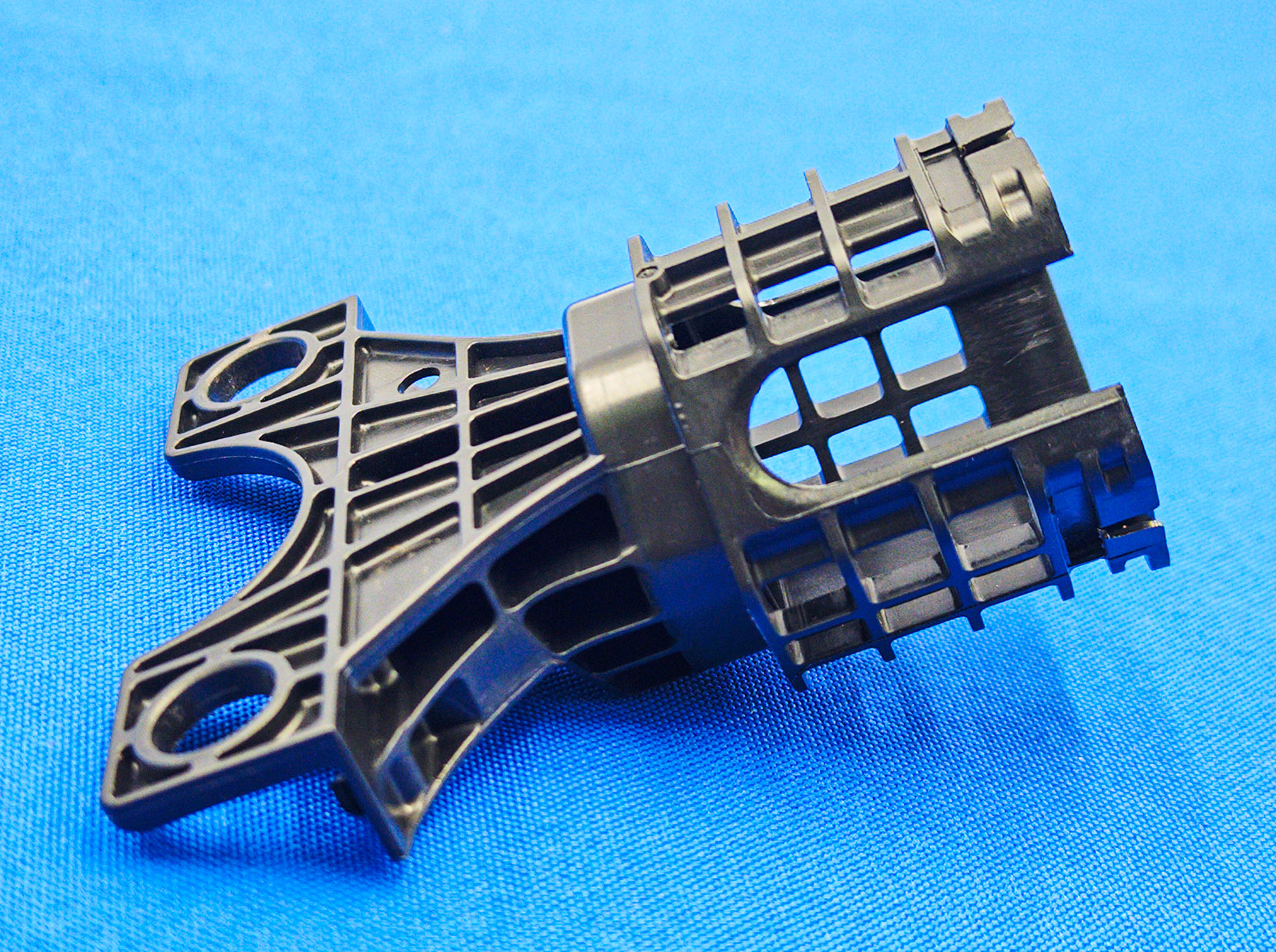
General Introduction:1 prototype injection mold for bridge production
Industry:Industrial product
T1 Samples’ Lead Time: 25 days
General Tooling Price:USD 4,000
Maximum Part Size:170*100*80mm
Part Material: PC+ABS
Tooling Life Time:50,000 cycles
Tooling Material:P20/P20
Tooling Structure:Manual insert, sliders, cold runner
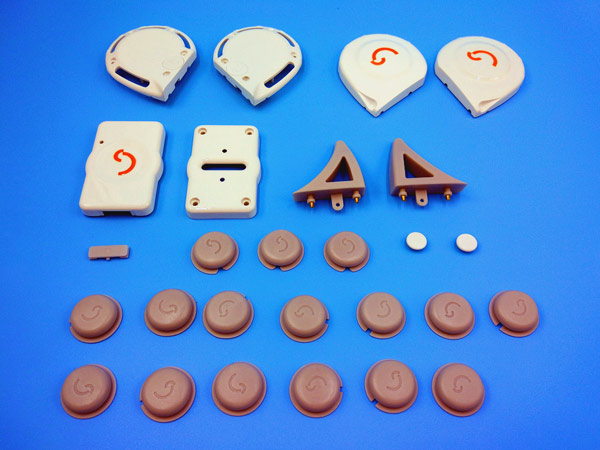
General Introduction:Biology from prototype to prototype mold making
Industry:Biology product
T1 samples’ Lead Time:25days
General Tooling Price:USD 10,000
Maximum Part Size:250*40*25mm
Part Material:ASA
Tooling Life Time:50,000 cycles
Tooling Material:P20/P20
Tooling Structure:Manual insert, sliders, cold runner
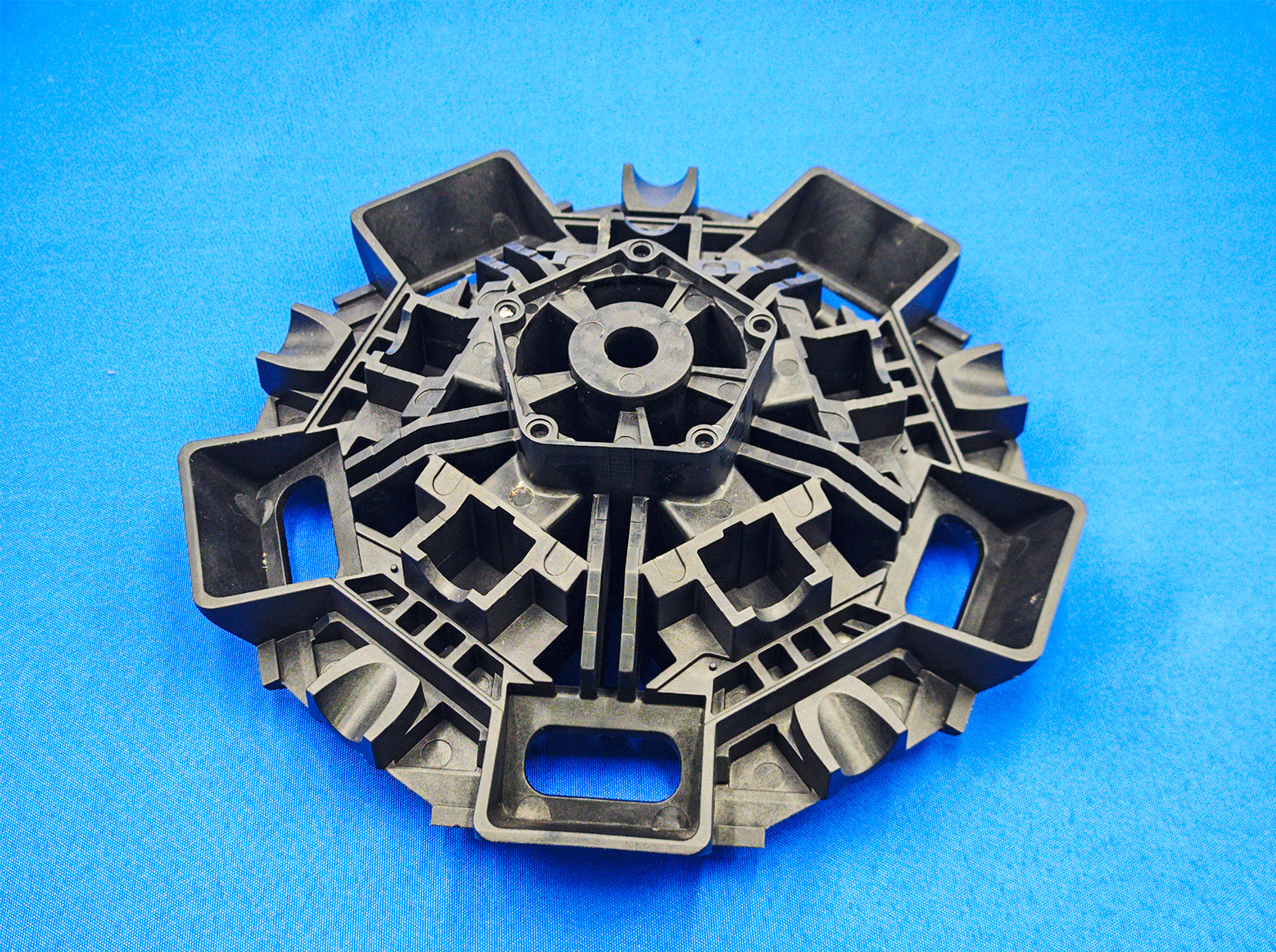
General Introduction:Prototype mold for low volume production
Industry:Industrial product
T1 samples’ Lead Time:25days
General Tooling Price:USD 10,000
Maximum Part Size:300*300*100mm
Part Material:PA66+40%GF
Tooling Life Time:5,000 cycles
Tooling Material:#50/#50
Tooling Structure:Manual insert, sliders, cold runner
Prototyping Injection Molding Cost Factors
For prototyping injection molding projects, normally we would expect the injection molding tooling cost at a reasonable low price, as it’s for market testing. Meanwhile, we would also expect the tooling developing lead time fast, so that we could launch the produce earlier to the market. Besides the production quantity requirement, there will be other injection molding cost factors. It’s especially the tolerance & the surface finish.
For example, a clear part would require NAK80 insert tooling steel. Strict tolerance or with many tolerances would require more reliable tooling structure. Especially for automotive industries, the inspection standard also maybe a significant cost factor. Following would be a series cost factors to prototyping injection molding tooling & parts .
They will generally affect the injection molding tooling & molded part cost.
Cost Factors of an Injection Mold:
- Lead Time
- Tolerance
- Inspection Standard
- Surface Quality
- Tooling Life Time
- Tooling structure
- Batch Production Quantity
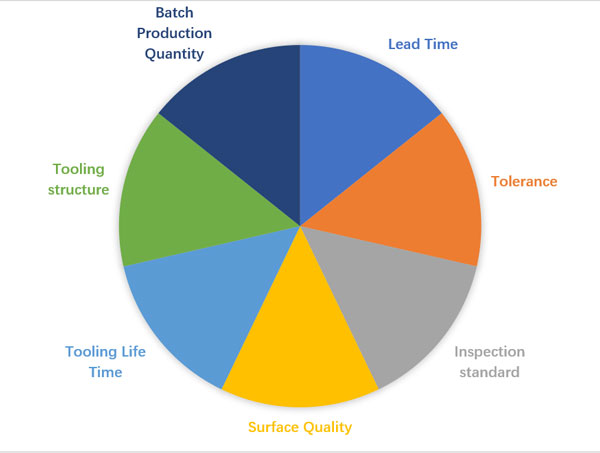
From the view of a plastic injection molding manufacturer, we would hope that our customers could provide the information to us as many as possible.
So that we could provide a more accurate injection molding quote, being with a suitable profit & competitive.
And also, we could have more open mind to negotiate with our customer, for a better approach.
Besides the general information requirement for the plastic injection molding projects:
- 3D drawings (in format of STEP, IGES, or X_T );
- Quantity needs; (batch or general needs);
- Part material; (if with specific grade or not);
- Surface finish Requirement;
We would also hope that the customer can provide more information for our estimation. For example:
- 2D drawings (it would be strongly requested, unless not available);
- General assembly (if available & feasible. Sometimes a clear general assembly view would allow us to provide more suitable suggestions)
- Part application or circumstance
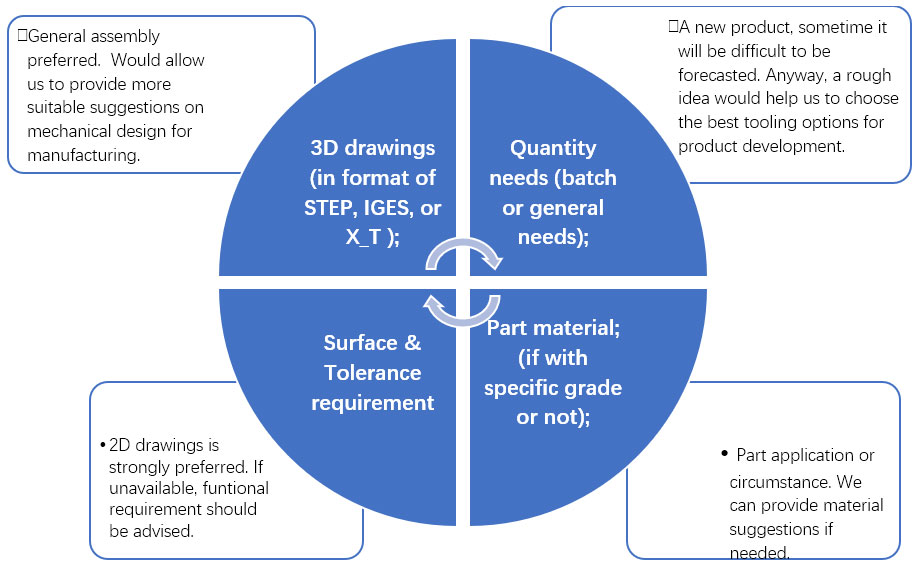
With them, we will have a better idea at the project, and will use our experience to negotiate with our customer.
We will try to apply our experience & professional to provide suggestions, mechanical adjustment and etc. So that our prototyping injection molding project will be cost efficiency and benefit our customers.
DFM Analysis
At prototyping injection molding projects, we would have to consider all the general DFM consideration.
Besides, there are some extra DFM considerations. They are especially for prototyping injection molding jobs.
Following would be some of our experience at DFM analysis.
Draft a Bit Bigger Than Production Tooling
Our consideration:
For prototyping injection molding tooling, generally we would suggest about 0.5 degrees larger than production tooling.
As the simplified tooling structure, for example the common mold base, manual inserts, the stability of prototyping tooling normally is not as good as the production tooling.
If the external surface with cosmetic requirement, for example glossy or texture, scratches will be easier to happen at the prototyping injection molding tooling.
A slightly large draft would allow us to develop tooling & injection molding parts with good quality within a challenging lead time.

Parting Line Not at the Cosmetic Surface
Our consideration:
For prototyping tooling, the injection molding tooling strength & tooling structure is not as good as production mold.
If the parting line at the cosmetic surface, when the flashes come out, it will easily hurt the cosmetic surface, and cause high scrap & injection molding cost.
It’s especially for the speaker holes, and venting holes.
For them, we would suggest the parting lines at the inner side, or at the cross section of the holes if with de-mold concern.
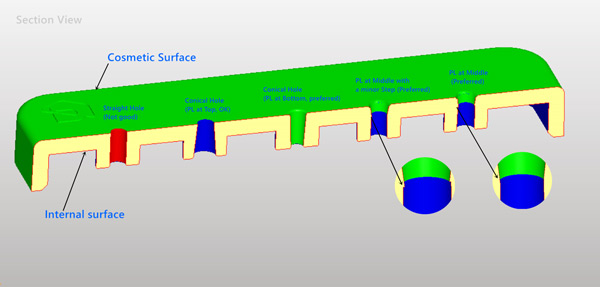
A More Reliable Injection Molding Gate for Cosmetic Parts
Our consideration:
As the low-volume production requirement, simplified cooling system, simplified tooling structure, and aggressive tooling developing lead time, we don’t suggest using injection molding gates with limited material flow: For example, submarine gate, banana gate.
Instead, we would suggest using some the gates with bigger size. They are better for material flow.
For example, edge gate, fan gate, pin-point gate of a 3-plate mold.
It will provide a larger production window for good-quality injection molding parts.
It’s not a must anyway.
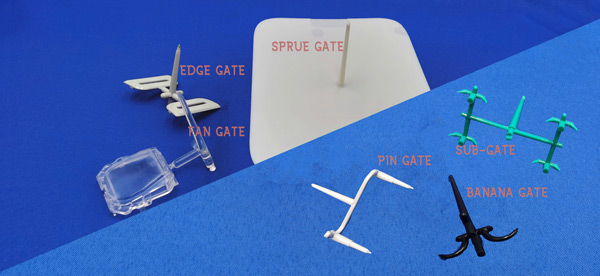
Are you working on a new plastic injection molding project? Looking forward to launching it at the market as early as possible?
Have a try at our Prototyping Plastic Injection Molding service.