In the ever-evolving landscape of product development and manufacturing, the key to success lies in creating products that capture attention, deliver exceptional performance, and seamlessly align with your brand’s vision.
While standard injection molding can be a viable option for mass production, custom injection molding offers a superior solution for businesses aiming to achieve unparalleled design flexibility, a wide range of material choices, and long-term cost-efficiency. By embracing custom injection molding, you open doors to endless possibilities, allowing you to bring your most innovative and intricate product designs to life while ensuring the highest quality and functionality standards.
This method empowers you to tailor every aspect of your product, from its shape and size to its material composition, resulting in a unique offering that sets you apart from the competition. Moreover, the long-term cost benefits of custom injection molding make it an attractive choice for businesses looking to optimize their production processes and maximize their return on investment.
What Sets Custom Injection Molding Apart?
At its core, custom injection molding is a specialized process where a mold is meticulously designed and fabricated to match the precise contours and intricacies of your unique product design. Unlike generic molds used for high-volume production, custom molds are tailored to your exact specifications, opening up a world of possibilities for your product’s form and function.
Key Advantages of Custom Injection Molding
- Design Freedom Unleashed:
Custom injection molding is a playground for innovation. You’re not bound by the limitations of pre-existing molds, allowing you to bring your wildest design concepts to life. Whether complex geometries, intricate details, or unique features set your product apart, custom molds empower you to achieve the perfect aesthetic and functional balance.
- Material Diversity for Optimal Performance:
With custom injection molding, you gain access to a wide spectrum of materials beyond the standard plastics typically used in mass production. You can select the ideal material to optimize your product’s performance, durability, and environmental impact. These include high-performance engineering resins, bio-based polymers, specialty composites, and more.
- Cost-Efficiency in the Long Run:
While the initial investment for a custom mold might be higher than using an existing one, the long-term benefits are substantial. Custom molds are engineered for high-volume production, resulting in significant cost savings per unit as your production scales. Moreover, optimizing your design for efficient manufacturing through techniques like Design for Manufacturing (DFM) can further reduce costs and streamline production.
- Enhanced Product Differentiation:
In today’s competitive marketplace, differentiation is paramount. Custom injection molding enables you to create products that stand out from the crowd, captivating customers with unique designs, features, and functionalities. This heightened differentiation can lead to increased brand recognition, customer loyalty, and a stronger market position.
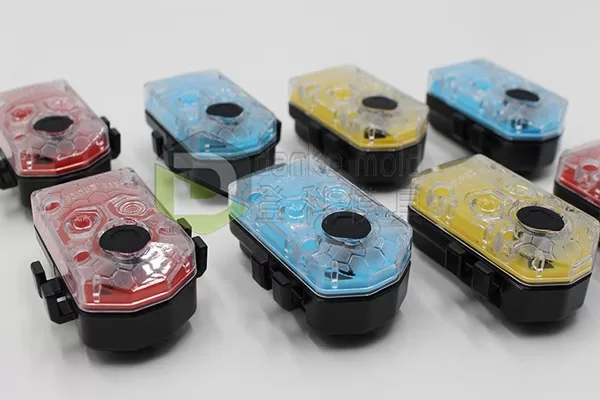
Injection molding parts
When Custom Injection Molding Shines
Custom injection molding is particularly well-suited for scenarios where:
- Unique Design Requirements: Your product has intricate features or complex geometries that standard molds can’t achieve.
- Specialized Materials: You need specific material properties, such as high heat resistance, chemical resistance, or biocompatibility, that are not readily available in mass-produced plastics.
- High-Volume Production: You anticipate producing a large quantity of your product, making the long-term cost-efficiency of custom molds advantageous.
- Market Differentiation: You want to create a product that stands out from competitors and resonates with your target audience.
The Custom Injection Molding Process
The journey from concept to reality with custom injection molding involves several key steps:
- Design Collaboration: You’ll work closely with experienced engineers and designers to refine your product concept and ensure it’s optimized for manufacturability.
- Mold Design and Fabrication: Skilled toolmakers will create a precision mold tailored to your product’s specifications.
- Material Selection: You’ll choose the ideal material based on your product’s requirements and desired properties.
- Production and Quality Assurance: The mold will produce your parts, with rigorous quality checks to ensure consistency and adherence to standards.
Partnering for Success
In product development and manufacturing, selecting the right custom injection molding partner can significantly influence the outcome of your project. Collaborating with a company with a proven track record of delivering exceptional results and exceeding client expectations is paramount.
Seek out a partner who demonstrates expertise in working with a wide range of materials, as this versatility ensures that they can accommodate your specific project requirements and recommend the most suitable options for your product. Furthermore, a strong commitment to quality and innovation indicates a partner who consistently strives for excellence, employing cutting-edge technologies and industry best practices to deliver superior products.
Entrusting your project to a reputable and experienced custom injection molding partner can ensure that they can bring your vision to life with precision, efficiency, and a focus on achieving optimal outcomes.
Embracing the Power of Custom Injection Molding
Custom injection molding is a game-changer in a world where customization and personalization reign supreme. It empowers you to create products that resonate with your target audience, elevate your brand, and drive your business forward. By choosing custom injection molding, you’re not just creating a product; you’re crafting an experience, a story, and a legacy that will endure for years to come.
If you’re ready to take your product to the next level, consider the transformative power of custom injection molding. Partner with a reputable injection molding company that shares your passion for innovation and excellence, and together, you can create products that redefine what’s possible.