Generally, there are two main methods of producing prototypes. They are additive manufacturing process and CNC machining. It appears that there are no dominating processes for all rapid manufacturing applications, so we noticed that, people who want to proceed their design into reality sometimes actually don’t know which alternative process is better. Here we would like to share our opinions/experiences with all of you. Hope it gives you some good ideas.
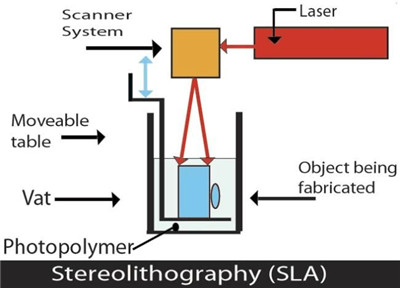
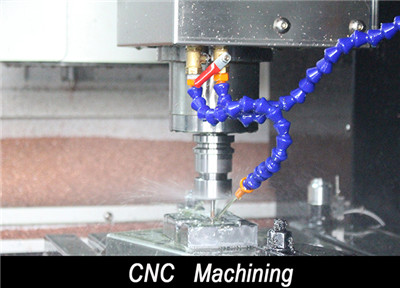
Most additive processes like SLA, SLS, present no geometry limitations. The ability to produce almost tiny features like sharp corners using additive processes makes them a desirable candidate for almost any geometries. For some complex components, it usually needs sectioning into two or more pieces in order to meet the manufacturability requirement if it was made by CNC machining, and then the pieces will be glued together to be a “completed” part. But if it was made by SLA or SLS, it’s not necessary to consider these issues.
However, some of other limitations, such as material limits, dimensional accuracy, surface finish and cost effectiveness limit the use of additive processes.
For the materials, the most common used ones for SLA are Somos14120 (opaque) and Somos 11122 (transparent). They are similar to ABS, but not that strong, and it is brittle, so it is easy to break. If you are designing thin and long components that are made by SLA, the result might not be ideal. Somos 11122 is not so transparent as acrylic, and it is difficult to polish it to be optical level.
For dimensional accuracy, actually the SLA tolerance can be achieved to +/-0.1mm, but if the part was exposed in the air for long time, it will absorb the water and then deform.
For surface finish, SLA is smooth, but SLS part is rough and difficult be sanded and polished.
For cost, SLA and SLS’s cost mainly depends on the weight of the part, so if your part is heavy and not so complex, CNC machining might be cheaper.
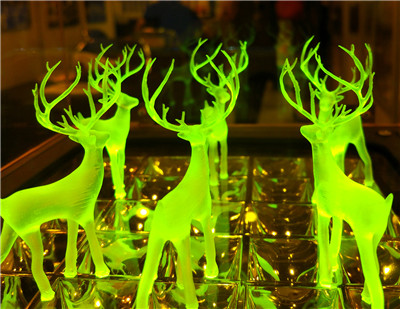
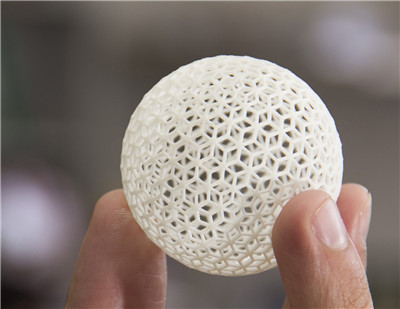
On the other hand, subtractive processes like CNC machining can create parts in a wide array of the most widely used materials to a very high accuracy. Rough machining to +/- 0.05mm is typical, while finish machining can achieve +/- 0.01mm, a combination which is not readily seen in other commercial RP processes.
However, CNC machining is limited to a simpler set of part geometries. Unlike other RP methods, CNC is a subtractive process, which requires a line of sight for the cutting tool. It’s impossible to machine hollow parts and undercuts require specialized tools and/or many re-fixture operations. Small inside corner radii also cause a problem for machining without using specialized tools. For metal parts, we usually create sharp corners by EDM (electrical discharge machining). For plastic parts, we can make it with special tool by hand.
Process planning for CNC machining requires a lot of work from a highly skilled technician, including developing a process plan, making tooling decisions, and designing a fixture scheme. Although CAM software makes the process faster and easier for a machinist, it is often not readily usable by engineers and other designers. This is one of the most significant hurdles has kept CNC away from serious consideration as an RP tool.
Here is an example to show one of the selection criteria between SLA (additive RP process) and CNC machining:
Figure: Example models with low (A) and high (B) mass/enclosed volume

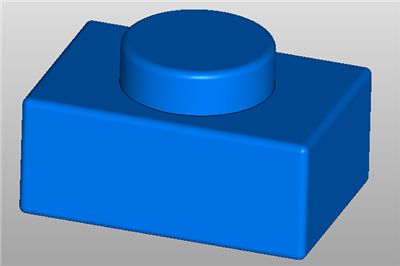
Due to the nature of the manufacturing processes, whether subtractive (CNC machining) or additive, different processes have their own innate advantages and disadvantages. Figure below illustrates an example of two parts with different mass volumes. The part in Figure (A) would require an excessive amount of material removal to make the part from a block of stock. This would be reasonably efficient for an additive RP process. On the other hand, for the part in Figure (B), an additive RP process would spend an excessive amount of time stacking simple layers, whereas the CNC machining process would finish the part very quickly from a block of stock.
Conclusion:
What type of parts are suitable for SLA process?
1 Complex structure but small size.
2 Light weight.
3 Parts to be made completed without sectioning.
4 Very short lead time required.
What type of parts are suitable for CNC process?
1 Simple structure but heavy.
2 High accuracy required.
3 Material required in detail that SLA cannot supply.
4 Simulate functional testing required.