Disposable medical device manufacturing involves producing single-use tools and instruments designed for safety and hygiene in healthcare. You rely on this manufacturing process to deliver sterile, high-quality devices efficiently, especially when volume manufacturing is crucial for meeting the enormous demands of the healthcare industry. The focus is on precision and consistency to prevent contamination and ensure patient safety.
When your needs require large quantities, volume manufacturing becomes a critical factor. It enables scalable production without compromising the strict quality standards that disposable medical devices must meet. This balance helps keep costs manageable while supporting the healthcare industry’s rapid pace and evolving requirements.
Key Processes in Disposable Medical Device Manufacturing
Manufacturing disposable medical devices involves precise techniques to meet strict quality and safety standards. You need efficient processes that ensure both high-volume output and consistent product integrity, especially for sterile, single-use components.
Injection Molding for Disposable Medical Devices
Injection molding is crucial for creating disposable parts with exact dimensions and durability. You control material flow by injecting medical-grade plastics into molds, which solidify into components like syringes or catheters. This method supports high-volume medical component production by enabling fast cycle times and repeatability.
You must choose specialized molds designed for medical use, often requiring polishing and venting to prevent defects. Consistent temperature and pressure ensure parts meet regulatory standards. This method reduces waste and supports complex geometries, which are vital for device functionality.
Automated Production and Sterilization
Automated lines streamline the assembly and sterilization of disposable devices. You integrate robotics for handling and packaging to reduce contamination risks and improve efficiency. Automation supports the automated production of sterile medical disposables, ensuring parts are assembled and sealed in controlled environments.
Sterilization methods—such as gamma irradiation, ethylene oxide, or electron beam—are incorporated directly into production or packaging steps. These processes validate sterility without compromising material properties. Automation boosts throughput and reduces human error, which is critical for meeting the demands of volume manufacturing.
Mass Production Techniques and Scalability
Volume manufacturing requires techniques that adapt quickly to changing demand, especially during health emergencies. You can scale production using modular equipment and flexible manufacturing cells designed for disposable medical devices.
Methods such as continuous injection molding, paired with automated inspection systems, ensure product uniformity at scale. You also benefit from maintaining multiple production lines or contract manufacturing partners to ramp up output rapidly for pandemic-ready supplies. Efficient resource allocation and supply chain management play key roles in scalable production.
Ensuring Cost-Effectiveness and Quality
Balancing affordability with high standards is crucial in the manufacturing of disposable medical devices. You must optimize production processes while maintaining compliance to reliably meet healthcare demands.
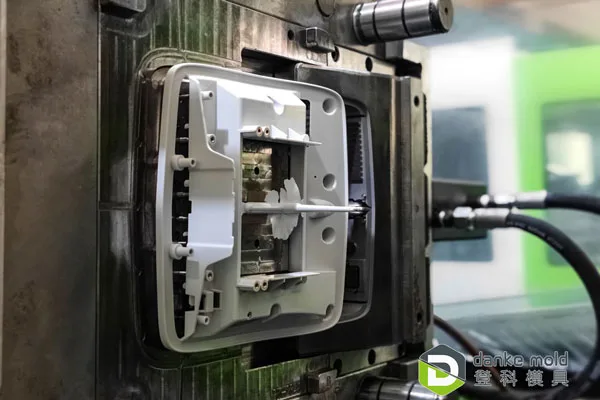
Injection molding parts
Strategies for Cost-Effective Manufacturing
To achieve cost-effective disposable healthcare products, focus on selecting materials and optimizing process efficiency. Using polymers with high availability and low cost, such as polypropylene or polyethylene, allows you to keep expenses manageable.
Automating assembly lines reduces labor costs, errors, and production time. You should also minimize waste through optimized mold designs and precise cutting techniques. Economies of scale help lower unit costs by spreading fixed expenses across large volumes.
Consider forming supplier partnerships to secure raw materials at consistent and competitive prices. Continuous process improvements, such as lean manufacturing principles, can further eliminate unnecessary steps, thereby reducing overhead without compromising quality.
Producing Single-Use Medical Tools at Scale
Volume manufacturing is crucial for meeting demand for single-use tools, such as syringes or catheters. You can leverage injection molding and blow molding for efficient, repeatable production of plastic components.
Setting up production with high-capacity machines allows you to run longer batches and reduce downtime. Achieving consistent output requires closely monitoring equipment maintenance to prevent defects.
Using modular tooling and interchangeable parts enhances flexibility, allowing for quick switching between product lines. Scaling up demands precise scheduling and inventory management to avoid bottlenecks and maintain a steady supply.
Quality Control and Regulatory Compliance
You are required to follow strict standards such as ISO 13485 and FDA regulations for disposable medical devices. Implementing a robust quality management system (QMS) ensures all products meet safety and performance criteria.
Quality control includes regular testing of raw materials, in-process inspections, and final product evaluations. Automated inspection systems using vision technology detect defects early, preventing faulty devices from reaching users.
Documenting every step of production supports traceability and audits. Staying updated on regulatory changes will help you adapt processes and certifications promptly, minimizing compliance risks.