In today’s rapidly evolving product development landscape, low-volume manufacturing is crucial in specialized products, prototype development, and niche market applications. Amid supply chain disruptions and market uncertainties, low-volume manufacturing offers remarkable flexibility that high-volume methods simply can’t match. Focusing on smaller production quantities—typically from dozens to a few thousand units—low-volume manufacturing provides distinct advantages in customization, time-to-market, and risk management that have become increasingly valuable in our volatile global marketplace.
Understanding the Strategic Value of Low-Volume Production
Low-volume manufacturing provides strategic advantages that have become significant as companies navigate uncertain economic conditions. Product development cycles benefit significantly from low-volume manufacturing capabilities, allowing you to test market acceptance before committing to costly high-volume tooling and production contracts. This low-volume manufacturing risk mitigation aspect enables more agile product development and market responsiveness—critical capabilities when consumer preferences and supply chains can shift overnight.
Industries with naturally limited demand, such as aerospace, specialized medical devices, and luxury goods, have long relied on low-volume manufacturing methods. However, we’re now seeing more mainstream sectors adopt low-volume manufacturing strategies to reduce inventory risk and maintain flexibility. The economics of low-volume manufacturing differ fundamentally from mass production, with greater emphasis on skilled labor, flexible equipment utilization, and adaptable processes rather than dedicated automated systems optimized for a single product.
Process Selection and Technology Options in Today’s Manufacturing Environment
Selecting appropriate processes represents a critical decision in low-volume manufacturing planning, especially as technology options evolve rapidly. While high-volume production typically commits to a single optimal process, low-volume manufacturing may employ hybrid approaches that balance tooling costs, labor requirements, and quality considerations. These decisions significantly impact low-volume manufacturing projects’ overall economics and timelines, particularly when navigating global supply constraints.
CNC machining is a cornerstone of low-volume manufacturing due to its exceptional versatility and minimal tooling requirements—advantages that have become even more valuable amid supply chain uncertainties. Similarly, additive manufacturing technologies have revolutionized specific segments of low-volume manufacturing by eliminating tooling for some applications, enabling on-demand production anywhere in the world. Traditional processes, including casting, molding, and forming, remain relevant in low-volume manufacturing when modified with adaptable tooling and setup approaches that minimize upfront investment.
Tooling Strategies for Cost-Effective Production
Tooling represents a significant consideration in low-volume manufacturing economics, especially as material and labor costs fluctuate globally. Unlike high-volume production, where tooling costs are amortized across millions of units, low-volume manufacturing requires approaches that minimize initial tooling investment while maintaining acceptable part quality.
Soft tooling, rapid tooling, and hybrid mold solutions often provide ideal solutions for low-volume manufacturing applications in today’s market environment. These approaches deliver faster lead times and lower initial costs than production tooling, aligning well with the economic realities of low-volume manufacturing and reducing financial risk. Modular and adaptable tooling designs also enhance flexibility in low-volume manufacturing environments, allowing for cost-effective product variations and modifications without major retooling expenses.
Quality Management and Validation Approaches for Global Compliance
Quality assurance in low-volume manufacturing contexts often differs significantly from high-volume approaches, requiring strategies that ensure compliance across diverse international markets. While mass production relies heavily on statistical process control and automated inspection, low-volume manufacturing may implement more intensive part-level inspection protocols. This comprehensive approach ensures quality without requiring the extensive process validation typical in high-volume environments.
Documentation and traceability are increasingly important in low-volume manufacturing, particularly in regulated industries serving global markets. Low-volume manufacturing operations typically maintain detailed records for each production batch, including material certifications, process parameters, and inspection results. This comprehensive documentation supports regulatory compliance across different jurisdictions and facilitates problem-solving when issues arise in low-volume manufacturing contexts.
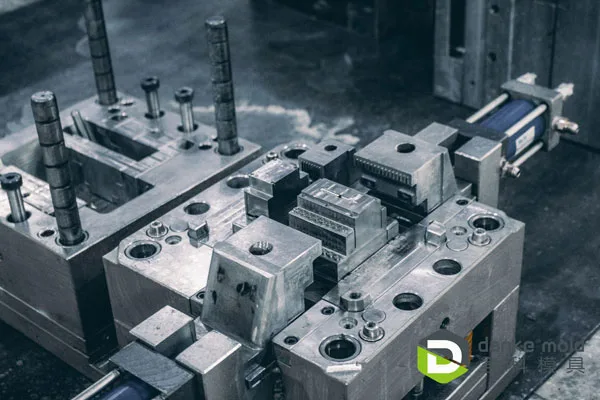
Rapid tooling machines
Your Expert Partner for Global Low-Volume Manufacturing
With our extensive engineering knowledge in low-volume manufacturing, rapid prototyping, and silicone molding, Danke Mold delivers precise, cost-effective solutions for companies worldwide. Our Design For Manufacture (DFM) assessments ensure every project maximizes quality and efficiency—we don’t just follow your CAD files; we optimize every aspect of your design for successful low-volume manufacturing.
As overseas outsourcing evolves in response to changing economic conditions and supply chain challenges, our low-volume manufacturing expertise offers significant advantages. Our facilities feature versatile production capabilities and skilled technical teams that understand the unique requirements of low-volume manufacturing projects. We’ve developed streamlined communication processes that ensure seamless collaboration across time zones.
Whether you need functional prototypes, specialized components, or bridge production while setting up high-volume manufacturing, our rapid tooling expertise means no job is too complex or time-sensitive. Contact Danke Mold today for a consultation and discover how our global low-volume manufacturing capabilities can transform your specialized production needs into competitive advantages!
Process Selection and Technology Options
Selecting appropriate processes is a critical decision in low-volume manufacturing planning. While high-volume production typically commits to a single optimal process, low-volume manufacturing may employ hybrid approaches that balance tooling costs, labor requirements, and quality considerations. These decisions significantly impact the overall economics and timeline of low-volume manufacturing projects.
CNC machining is a cornerstone of low-volume manufacturing due to its exceptional versatility and minimal tooling requirements. Similarly, technologies like 3D printing have revolutionized specific segments of low-volume manufacturing by eliminating tooling for some applications. Traditional processes, including casting, molding, and forming, remain relevant in low-volume manufacturing when modified with adaptable tooling and setup approaches.
Tooling Strategies for Cost-Effective Production
Tooling represents a significant consideration in low-volume manufacturing economics. Unlike high-volume production, where tooling costs are amortized across millions of units, low-volume manufacturing requires approaches that minimize initial tooling investment while maintaining acceptable part quality.
Soft tooling, rapid tooling, and hybrid mold solutions often provide ideal solutions for low-volume manufacturing applications. These approaches deliver faster lead times and lower initial costs than production tooling, aligning well with the economic realities of low-volume manufacturing. Modular and adaptable tooling designs enhance flexibility in low-volume manufacturing environments, allowing for cost-effective product variations.
Quality Management and Validation Approaches
Quality assurance in low-volume manufacturing contexts often differs significantly from high-volume approaches. While mass production relies heavily on statistical process control and automated inspection, low-volume manufacturing may implement more intensive part-level inspection protocols. This comprehensive approach ensures quality without requiring the extensive process validation typical in high-volume environments.
Documentation and traceability are increasingly important in low-volume manufacturing, particularly in regulated industries. Low-volume manufacturing operations typically maintain detailed records for each production batch, including material certifications, process parameters, and inspection results. This comprehensive documentation supports regulatory compliance and facilitates problem-solving when issues arise in low-volume manufacturing contexts.
Personnel and Workforce Considerations
The human element plays a particularly crucial role in successful low-volume manufacturing. Unlike highly automated mass production, low-volume manufacturing relies more heavily on skilled technicians and operators who understand multiple processes and can adapt to changing production requirements. These personnel represent a key competitive advantage in low-volume manufacturing environments.
Training and skill development become strategic in low-volume manufacturing organizations. Cross-training enables the workforce flexibility needed to handle the diverse requirements of low-volume manufacturing. Additionally, experienced personnel in low-volume manufacturing environments develop valuable institutional knowledge about product-specific nuances that often prove crucial to quality and efficiency.