As the manufacturing industry becomes more and more competitive, we must keep production efficiency at an all-time high while minimizing production costs. One technology that has transformed the game and provided manufacturers with the chance to reach those goals is the digital twin.
Digital twins offer a virtual representation of the physical manufacturing process that has never been possible before, enabling major improvements in productivity, quality, and cost from the plant floor to the operation of the individual devices.
What Exactly Are Digital Twins?
Imagine having a real-time, virtual copy of your entire production line, equipment, and processes at your fingertips. Which is basically what a digital twin offers, such as sensors, cameras, and IoT devices. These digital twins replicate real-world operations. The result is a full three-dimensional simulation of your factory in real time, whereby you can track, analyze, and optimize every facet of your production line.
Reaping the Rewards: Benefits for Volume Manufacturing
Companies who have adopted digital twins into their volume manufacturing operations find that they benefit from many things, such as:
- Reduced Downtime: By providing real-time insights into equipment performance, digital twins enable predictive maintenance, reducing unplanned downtime by up to 25%.
- Lower Maintenance Costs: With adaptive optimization of maintenance schedules using real-time data and simulations, I can cut down my costs by 20%.
- Increased Production Output: Identifying and addressing bottlenecks through virtual simulations can boost production output by up to 15%.
- Improved Quality: Early detection of potential quality issues through real-time monitoring and simulations can decrease defect rates by 30%.
Transforming Production: How Digital Twins Make a Difference
Digital twins revolutionize production processes in several key ways:
- Real-time Monitoring: With digital twins, you get a holistic perspective of your whole production line. You can see it all happening as it happens. This allows equipment breakdowns or process upsets to be foreseen in advance before they become production downtime or costly defective products. For example, an auto parts company was able to anticipate and prevent breakdowns of its machinery using digital twin technology, which saved it $3.5 million in only one year.
- Risk-Free Testing: Would you like to try new production arrangements or process modifications? A digital twin, allowing for experimentation in a virtual world without high risk and costs. You can practice with different scenarios and see what would happen without affecting real production! One major consumer electronics company ran 50 line configurations through its digital twin before actually modifying a single physical configuration and saving weeks of downtime.
- Enhanced Training: Digital twins offer a valuable tool for training new operators and upskilling existing employees. With realistic simulation environments, they can use the equipment, troubleshoot, and complete complex operations without the fear of breaking a machine and losing some outlandish amount of money. One aerospace company claimed to have decreased training time by 60% by using digital twin simulations for intricate assembly routines.
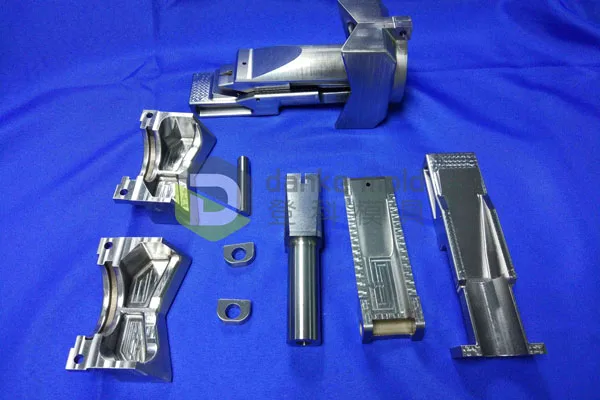
CNC SUS 304
Implementing Digital Twins: A Step-by-Step Approach
While the concept of digital twins may seem daunting, implementing them doesn’t have to be an overwhelming task. Here’s a step-by-step approach to get started:
- Start Small: Start by focusing on a specific production line or a critical piece of equipment. This allows you to gain experience and demonstrate the value of digital twins before scaling up to the entire operation. A food packaging company successfully implemented a digital twin for its bottling line, achieving a 35% efficiency boost before expanding to other areas.
- Prioritize Data Collection: Install sensors and other data acquisition devices to collect key metrics, such as equipment performance, production speeds, quality measurements, and environmental conditions. This data will feed the digital twin and enable accurate simulations and analysis.
- Integrate with Existing Systems: Connect the digital twin to already existing systems such as production planning, maintenance, quality, or spare parts systems. By connecting in this way, data is no longer ‘siloed’, and the digital twin gains access to a larger picture of manufacturing as a whole.
Success in Action: A Real-World Example
A medical device manufacturer implemented digital twins for its clean room assembly lines, achieving impressive results within a year:
- Production volume increased by 40%
- Defect rates decreased by 45%
- Energy costs reduced by 30%
- Training time cut in half
In this case, the digital twin can be used to revolutionize production processes, increasing quality while lowering cost.
Looking Ahead: The Future of Manufacturing
As technology advances further, digital twins will become even more important in volume manufacturing. Companies that do not adopt this technology will give up a substantial competitive edge in terms of product quality, cost control, production flexibility, and worker safety.
If you are ready to enjoy the benefits that digital twins can bring to your manufacturing operation, start by mapping your current processes and look for areas where virtual simulation could bring the biggest improvements. Remember, digital twins are not just for large enterprises; small and medium-sized manufacturers can also gain by starting small and scaling up as they show results.
Need Help?
If you have questions about implementing digital twins in your facility or want to learn more about how this technology can optimize your volume manufacturing operations, contact Danke Mold today. Our team of experts can provide guidance and support to help you successfully integrate digital twins into your manufacturing strategy.