Ever picked up your smartphone case and wondered, “How on earth did they make this?” You’re holding the magic of plastic injection molding in your hands! This manufacturing superhero creates virtually everything from your kitchen gadgets to car parts with incredible precision. Let’s peek behind the manufacturing curtain to see how this remarkable process works—knowledge that might just transform your following product from “meh” to “amazing”!
The Science Behind Plastic Injection Molding: Manufacturing Alchemy
Think of plastic injection molding as cooking with plastic—but instead of an oven, imagine the world’s most sophisticated hot glue gun on steroids! The process begins with humble plastic pellets that get heated until they transform into a flowing river of molten polymer. This liquid plastic gets shot (yes, literally injected!) into a custom-designed mold cavity under pressure that would make your car tire jealous. Within seconds, the material cools, solidifies, and presto—out pops your finished part! This high-speed cycle makes plastic injection molding perfect for cranking out thousands of identical parts faster than you can count them.
The wizardry of plastic injection molding isn’t just about melting and cooling plastic—it’s a delicate dance of material science. Engineers obsess over flow dynamics (how the molten plastic moves), cooling rates (how quickly it solidifies), and shrinkage factors (how much it contracts). Getting these variables just right is why your phone case fits perfectly instead of looking like it melted in the sun. Today’s plastic injection molding pros even use computer simulations that predict how the plastic will behave, eliminating costly mistakes before a single part is made.
The Orchestra of Machines: Key Components Working Together
A plastic injection molding system is like a perfectly synchronized orchestra, with several instruments playing in harmony. The star performer—the injection unit—melts and delivers the plastic material with precision timing. Meanwhile, the powerful clamping unit (think industrial-strength vise) holds the mold closed against pressures that would make a hydraulic press sweat. The authentic prima donna is the mold itself—the most crucial element in plastic injection molding—crafted with meticulous detail to shape your product with micron-level precision.
Modern plastic injection molding machines aren’t just mechanical beasts—they’re smart, too! Today’s equipment comes packed with sophisticated control systems that monitor and adjust dozens of process parameters in real time, like a vigilant chef constantly checking temperature, pressure, and timing. These brainy machines ensure your millionth part looks identical to your first while squeezing maximum efficiency from every gram of material.
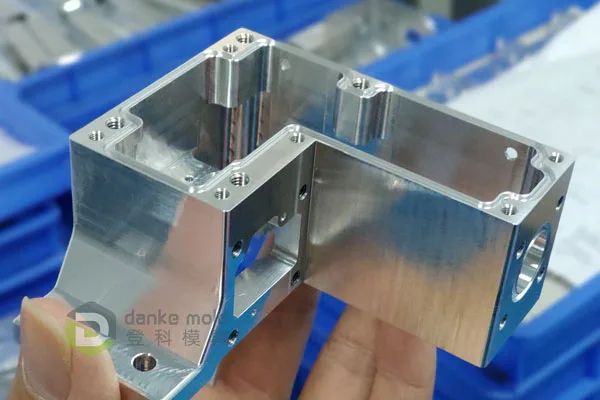
CNC machining products
Material Matchmaking: Finding Your Perfect Plastic Partner
The success of your plastic injection molding project often boils down to one critical decision: choosing the right plastic! It’s like dating—each material brings different qualities to the relationship. Need something rigid yet flexible for a phone case? ABS might be your perfect match. Creating food containers? Polypropylene brings food-safe properties to the table. With hundreds of materials available for plastic injection molding, finding your ideal plastic partner means considering strength requirements, chemical resistance, heat tolerance, and cost.
The material selection process for plastic injection molding is where science meets art. Your plastic needs to flow seamlessly through often tortuous mold cavities (think of threading a needle while wearing mittens—it’s that precise) and then cool to achieve the performance specifications your product demands. The right material choice in plastic injection molding can be the difference between a product that disappoints and delights.
The Cutting Edge: Advanced Techniques Pushing Boundaries
Plastic injection molding keeps evolving faster than smartphone technology! Today’s advanced techniques would seem like science fiction to earlier generations of manufacturers. Multi-material molding creates products with hard and soft sections in a single operation—think toothbrushes with rigid handles and soft grips. Like nature’s hollow bones, gas-assisted plastic injection molding creates hollow sections within parts, making them lighter yet stronger.
Other game-changing innovations in plastic injection molding include in-mold labeling, where your product gets decorated during formation rather than afterward—imagine baking the frosting inside the cake! For the medical and electronics industries, micro-molding takes plastic injection molding to microscopic levels, creating tiny components you’d need a microscope to inspect them. These advances keep pushing the boundaries of what’s possible in manufacturing.
Detective Work: Quality Control and Problem Solving
Even with all our technology, maintaining perfect quality in plastic injection molding requires Sherlock Holmes’ detective skills! Familiar villains include sink marks (depressions on surfaces), warping (twisting or bending), short shots (incomplete filling), and flash (excess material that escapes between mold sections). These culprits can ruin the look and function of your parts if not caught and corrected.
The true heroes of plastic injection molding are the experienced technicians who can read the subtle clues in a defective part like a detective reads a crime scene. They implement corrective actions to optimize the plastic injection molding process through temperature, pressure, or timing adjustments. Like maintaining a high-performance sports car, preventive maintenance of equipment and molds is essential for consistent quality and maximum uptime.
Ready to Transform Your Product Ideas into Reality?
With our engineering expertise in plastic injection molding and decades of hands-on experience, we turn challenging projects into manufacturing success stories. Our team doesn’t just push buttons—we dive deep into Design For Manufacture principles that extract maximum value from every mold we create. We don’t blindly follow CAD files; we enhance every aspect of your performance design that exceeds expectations.
Whether you’re developing consumer products, medical devices, or automotive components, our plastic injection molding capabilities handle complexities that would stump less experienced manufacturers. Our state-of-the-art machinery and passionate technicians deliver your plastic injection molding requirements with a precision that matters and the speed that keeps you ahead in today’s competitive market.
Ready to transform your product concepts from “good enough” to “absolutely perfect”? Contact us today for a quote and discover what happens when engineering excellence meets plastic injection molding mastery!