Liquid silicone rubber molding transforms how manufacturers create durable, flexible components across multiple industries. This advanced manufacturing process delivers exceptional precision and reliability for applications ranging from medical devices to automotive parts.
You need to understand why liquid silicone rubber molding outperforms traditional manufacturing methods. The process offers superior temperature resistance, biocompatibility, and dimensional stability that other materials simply cannot match.
What Makes Liquid Silicone Rubber Molding Superior to Traditional Methods
Liquid silicone rubber molding uses a two-part platinum-catalyzed system that creates stronger, more consistent parts than conventional rubber molding. The liquid state allows for complete mold filling, eliminating air pockets and ensuring uniform density throughout your components.
The curing process happens at elevated temperatures, typically between 150-200°C. This heat-activated reaction creates cross-linked polymer chains that give the final product its exceptional properties. Your parts will maintain flexibility across temperature ranges from -65°C to 200°C.
Liquid silicone rubber molding produces parts with Shore A hardness ranging from 10 to 80. This flexibility lets you create everything from soft gaskets to firm structural components using the same basic process.
Technical Process Behind Liquid Silicone Rubber Molding Operations
The liquid silicone rubber molding process begins with precise material preparation. Two liquid components mix in exact ratios, typically 1:1 or 10:1, depending on your specific formulation requirements.
Specialized injection molding machines handle the mixed material. These machines feature heated barrels that maintain optimal processing temperatures while preventing premature curing. The material flows through heated runners into your mold cavities.
Mold design plays a critical role in liquid silicone rubber molding. Your molds need proper venting to prevent air entrapment. Gate placement affects flow patterns and final part quality. Most molds use hot runner systems to maintain consistent temperatures throughout the cavity.
Cycle times vary based on part thickness and complexity. Thin-walled parts cure in 30-60 seconds, while thicker sections may require 2-3 minutes. The automated demolding process removes finished parts without operator intervention.
Key Applications Where Liquid Silicone Rubber Molding Excels
Medical device manufacturers rely on liquid silicone rubber molding for creating biocompatible components. Catheters, seals, and implantable devices benefit from the material’s inert properties and sterilization compatibility. The process meets USP Class VI and FDA requirements for medical applications.
Automotive applications include gaskets, seals, and vibration dampeners. Liquid silicone rubber molding produces parts that withstand engine compartment temperatures while maintaining sealing properties. The material resists automotive fluids like oil, coolant, and brake fluid.
Consumer electronics benefit from liquid silicone rubber molding for keypads, seals, and protective covers. The material provides excellent electrical insulation while offering tactile feedback for user interfaces. Its transparency allows for LED light transmission in backlit applications.
Aerospace components require materials that perform in extreme conditions. Liquid silicone rubber molding creates seals and gaskets that function at high altitudes and temperature extremes. The material maintains properties in both vacuum and pressurized environments.
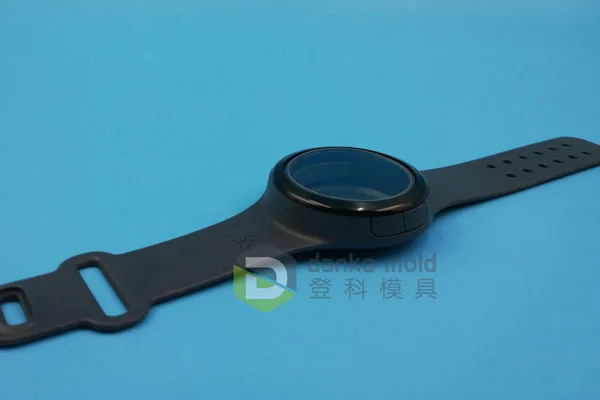
Silicone watch strap
Choosing Between Liquid Silicone Rubber Molding and Alternative Materials
Your volume requirements significantly impact material selection. Liquid silicone rubber molding becomes cost-effective at medium to high production volumes, typically above 10,000 parts annually. Lower volumes may benefit from alternative processes like compression molding or casting.
Part complexity favors liquid silicone rubber molding over other methods. The low viscosity liquid fills intricate details, thin walls, and complex geometries that solid rubber cannot achieve. Multi-component molding allows overmolding onto rigid substrates in a single operation.
Performance specifications drive material selection decisions. When you need superior temperature resistance, chemical compatibility, or biocompatibility, liquid silicone rubber molding often provides the only viable solution. Traditional rubber compounds cannot match these performance characteristics.
Cost considerations include both tooling and per-part economics. Initial tooling investment for liquid silicone rubber molding exceeds conventional rubber molding costs. The automated process and reduced labor requirements offset higher tooling costs at production volumes.
Future Developments in Liquid Silicone Rubber Molding Technology
Automation advances continue improving liquid silicone rubber molding capabilities. Robotic systems handle part removal, inspection, and packaging without human intervention. Vision systems detect defects and sort parts automatically.
New material formulations expand application possibilities. Conductive grades enable electronic applications, while flame-retardant versions meet stringent safety requirements. Self-healing formulations represent emerging technology for specialized applications.
Process monitoring technology provides real-time quality control. Sensors track injection pressure, temperature, and cure state throughout each cycle. This data enables predictive maintenance and consistent part quality.
Liquid silicone rubber molding offers unmatched versatility for precision manufacturing applications. The process delivers consistent quality, excellent material properties, and design flexibility that traditional methods cannot achieve. Your manufacturing success depends on choosing the right process for your specific requirements.
Looking for expert liquid silicone rubber molding manufacturing services? Contact Danke mold today to streamline your production process with professional outsourcing solutions tailored to your precision manufacturing needs.