Silicone molding is a versatile and widely used manufacturing process that involves creating molds from silicone rubber. This approach has several uses and benefits across various industries, including automotive, medical, consumer products, electronics, and more. Here are some of the primary uses and advantages of silicone molding:
What is Silicone?
Silicone is a synthetic polymer made of silicon, oxygen, carbon, and hydrogen. It has various forms, including fluids, gels, rubber, and resins, known for their versatility and unique properties such as heat resistance, flexibility, and durability.
Uses of Silicone in Molding
- Prototyping: Silicone molds are often used for rapid prototyping, allowing designers and engineers to quickly and cost-effectively create functional parts.
- Consumer Products: Silicone is widely used to create kitchenware, toys, and various household items due to its flexibility and durability.
- Medical Devices: Silicone is biocompatible and is frequently used to manufacture medical devices like tubing, implants, and other components that require stringent hygiene standards.
- Auto Parts: Silicone is used to produce seals, gaskets and a variety of components that are resistant to extreme temperatures and environmental conditions.
- Electronics: Silicone molds are used to mold and encapsulate electronic components, providing insulation and protection from moisture and dust.
- Jewelry and Crafts: Artists and hobbyists use silicone molds to create intricate designs in jewelry-making and other crafts.
- Food Production: Food-grade silicone molds are employed in baking and candy-making, allowing for the production of intricate shapes and easy release of baked goods.
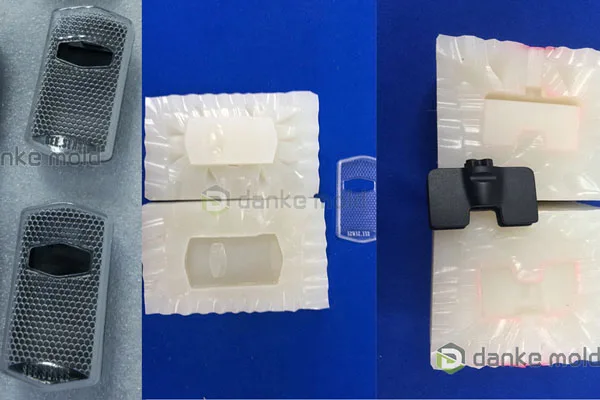
Vacuum casting products
Benefits of Silicone Molding
Businesses may get various advantages and a competitive edge by using silicone molding.
- Durability and Flexibility
Because silicone molds are flexible and long-lasting, they maintain their form and functionality even after several usage. They are thus ideal for large-scale manufacturing, which lowers expenses and boosts productivity.
- Resistance to Heat and Cold
Silicone is perfect for molding applications that need heat or cold since it can withstand very high or low temperatures. This guarantees dependable operation and superior goods, even under demanding circumstances.
- Versatility
Custom silicone molds enable manufacturers to quickly make intricate and elaborate pieces that fulfill unique design requirements. This promotes innovation and creativity in the creation of new products.
- Superior Surface Finish
The use of silicone molds results in uniform, smooth surfaces that need less post-processing. This improves the overall quality and look of the items while also saving time.
conclusion
Silicone molding is a practical and efficient method for the production of a wide range of products across various industries. Its unique properties and flexibility make it an increasingly popular option for manufacturers looking to balance quality, efficiency and cost-effectiveness.